National Safety Month: Rigging An Arter
- Ben Nordman
- Jun 18, 2021
- 3 min read
Updated: May 8, 2024
Moving is such an arduous task for any manufacturing company. The thousands of pounds that are a part of each machine proves as a tough task to safely complete. Arter Precision Grinding Machines are no different. With June being National Safety Month, knowing the proper techniques of lifting and rigging an Arter is an important safety procedure to have in your back pocket when moving becomes necessary.
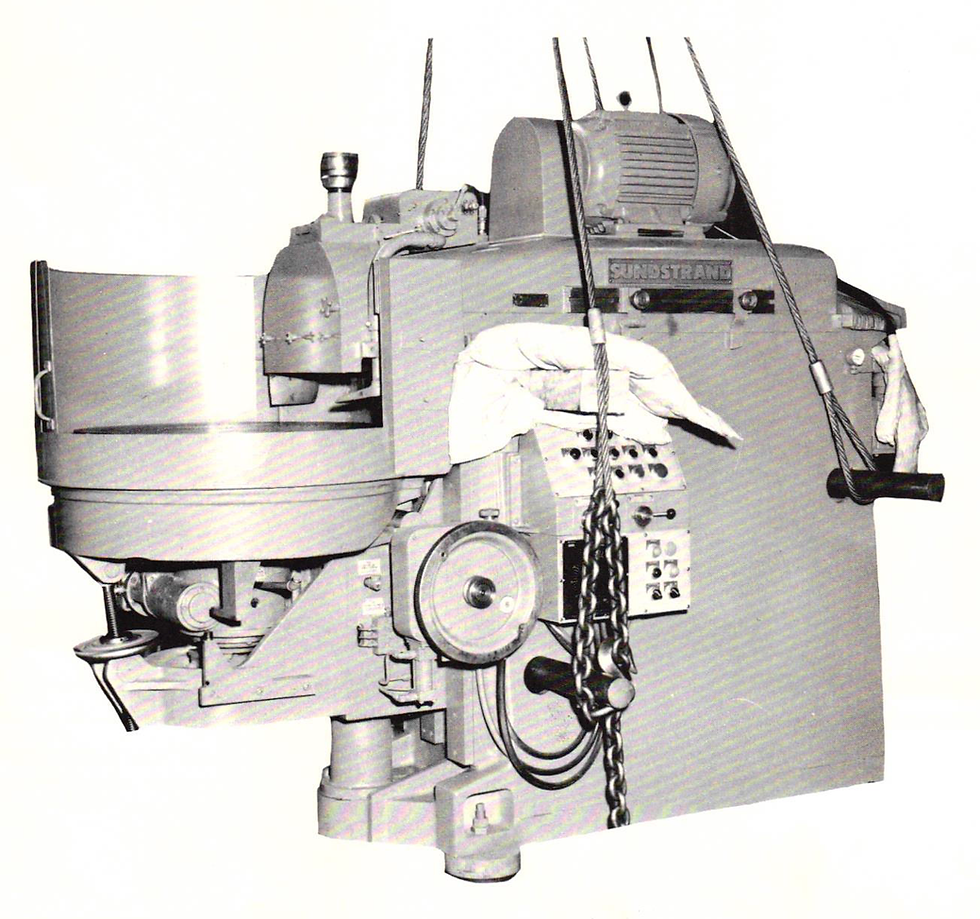
Back when Arter manuals were printed for older models, included in many of them were guides as to how properly lift one of the machines. While one might just say, "Well it has to be just how we lift our other machines" the reality is that there is a correct and incorrect way to lift all machines. Weight distribution, placement of lifting equipment, and complimentary lifting equipment such as chains are all necessary considerations when lifting an Arter.
The first step in preparing the Arter to be moved is to make sure the machine is no longer bolted to the concrete floor, if applicable. Depending on the model, most of the machines rest on three points, and each point needs to be detached before attempting to move.
Additional components that are attached to the machine that need to be removed are the coolant tank, all fluids drained, and any electrical components unplugged. This ensures that the machine is the only item being lifted and decreases the chances of injury.

From there, each model has it's own lifting procedure. As each model progressed, the lifting procedure changed, with each manual stating the proper way to lift. It is imperative that each time an Arter is moved, the manual is referenced.
There are some commonalities between each model, though, first starting with a four-point lift. To ensure the weight is evenly distributed, be sure that there are four points of lifting. In Picture 1, two points on the model H on the near side can be seen, with the cables on the other side also seen in the background. This should be done in each lift for each model.
Next, using an overhead crane is important when lifting. A common mistake that shops have when moving grinders is that they use a forklift. While it may seem easier, using a forklift could cause the machine to tip over because it is not being lifting straight up.
The location of the points of lifting is important when it comes to lifting as well. With Model H and newer, there are specific lifting holes which are pictured in Picture 1. In hydraulic models, you can see where to lift below. The use of those beams also makes sure the lifting is straight up and the weight is distributed correctly.

The last consideration that needs to be made is keeping the knee blocked. Making sure it does not jar when being moved is important to keeping the machine in working condition when it is replaced.
While any type of machine can be complicated and difficult to move, following these steps can help ease your pain. As a reminder, always reference the machine's manual for lifting instructions. Also, if there are still questions or if there is no manual for your machine available, give us a call at 815-962-8700 to get yours.
Next week is the last week of National Safety Month and we look to bring you the final safety tips for our #ObsidianMFG brand, Magna-Lock USA.

Obsidian Manufacturing Industries, Inc. is a Rockford, Ill. manufacturing company and is the OEM for Magna-Lock USA workholding, MagnaLift & Power-Grip lift magnets, and Arter Precision Grinding Machines as well providing surface grinding services. They are located at 5015 28th Ave. in Rockford, Ill. with a phone number of 815-962-8700. Check out more at obsidianmfg.com/brands.
Comments